自社の課題にマッチしたシステム導入が成功のカギ
“無駄”と“無理”の削減により生産性が飛躍的に向上
株式会社秋田マシナリー
取締役工場長
渡辺 一彦
さん
株式会社秋田マシナリー(外部サイトに移動)
精密板金加工製造業として、半導体製造関連装置や医療用検査装置の部品等を製造している「株式会社秋田マシナリー」。デジタル技術の活用による、業務の“無駄”と“無理”の削減に取り組みました。プロジェクトリーダーとして、デジタル技術の導入に取り組んだ渡辺さんはどのように課題に向き合い、いかに生産性を向上させることができたのでしょうか。
マンパワーに頼っていた業務をデジタル化
- 今回取り組まれたことを教えてください。
-
従来の管理体制を継続させるのではなく、時代に即した手法に転換。
大きく2つのことを行いました。
1つ目は、受注情報から生産指示情報への変換の手間を減らすために行った、Web-EDI(電子受発注システム)と連動した生産管理システムの導入です。2つ目が、進捗管理の効率化のために行った、バーコードリーダーやタブレットなどを活用した進捗管理の改善です。 - 取り組まれた経緯は。
-
複数の建屋に生産ラインがあるため、アナログな体制では管理者が生産状況を把握するのもひと苦労だった。
当社は、複数の工場で、多品種少量生産型の製造を行っています。これまでは紙ベースや人の目によるアナログなチェックを続けてきていましたが、年々受注量が増え続ける中、管理体制に限界を感じていました。 月に5千件以上にも及ぶ受託生産品の受注情報を、速やかにミスすることなく生産指示情報に変換して製造工程に流すことができれば、事務的な負担が大幅に削減されますし、受注から製造開始までのリードタイムを短縮することができます。また、進捗管理のための時間を削減できれば、生産にかける時間を増やすことができます。この2つの点で改善の余地があると考え取り組みました。 - 具体的な課題と改善方法について教えてください。
- 以前の体制を振り返ってみると、業務が非効率的であると同時に業務が属人化されていました。
受注工程においては、事務所にいる社員が、顧客から来る受注データを一つひとつ汎用表計算ソフトに手入力し、生産指示書等の書類を作成していました。手入力のため、時間がかかるとともに、入力ミスによる余剰生産や手配漏れなどのリスクがありましたが、Web-EDIと連動する生産管理システムを導入することにより、受注データから生産指示情報への変換を効率化しました。
生産工程においては、生産現場の社員が、各工程を終えた際に紙のチェックリストに進捗状況を記録していました。多品種少量生産のため、自分が担当している部品のチェックリストを探すのに時間がかかっていたほか、第一工場と第二工場が離れているため、管理者が進捗状況を把握するのも手間がかかっていました。この無駄な時間を削減するため、生産指示書にバーコードを付け、工場内に配置したタブレットとバーコードリーダーにより進捗状況を入力できるようにしたことで、進捗管理の効率化を図りました。
導入直後から期待以上の効果が表れる
- デジタル化にあたり、どんな困難がありましたか。
- 生産管理システムについてですが、市販されているパッケージソフトも検討しましたが、当社の業務や運用にはマッチしなく、カスタマイズ費用が高額になってしまうほか、多機能過ぎることが悩みの一つでした。さまざまなソフトウェアを対象に検討しましたが、身の丈にあった機能やアフターフォローなどを考慮して、県内の事業者に委託することを決めました。
- 「株式会社フィデア情報総研」に依頼したそうですね。
- そうですね。銀行様から紹介を受け、信頼できましたし、県内企業という安心感が何より大きいものでした。導入を決定してから本格的に稼働を始めるまで、3カ月というタイトなスケジュールでしたが、従来のシステムを活用して移行がスムーズに行えるようにとブラッシュアップを重ね、当社の業務内容に寄り添うソフトウェアを開発していただきました。アフターフォローにも真摯に応えてくれるので、ありがたいです。
- デジタル技術を導入してみていかがですか。
-
生産ラインに設置された大型ディスプレイ。工程ごとにバーコードを読み取ることで、作業員一人ひとりがリアルタイムにディスプレイで情報を確認・共有することができる。
受注情報処理の自動化により、属人化していた当該プロセスの生産性が1.5倍以上に向上しました。アナログだった受注から生産指示に情報を変換する作業は、デジタル化によって労働力や労働時間の削減につながっています。これまで、納期や工程に急な変更があった場合は残業などマンパワーに頼らざるを得ない状況でしたが、納期変更などの情報伝達がシステムにより自動化されたことにより、社員に無理をさせることが少なくなりました。世界的な半導体不足に伴う製造関連装置の増産や納期の変更、新型コロナによる医療用検査装置の増産など、状況の変化が激しい中、さまざまな要請に柔軟に対応できるようになっています。
また、生産現場や出荷場に配置したバーコードリーダー付きタブレット端末と大型ディスプレイにより、出荷までの進捗状況や納期の変更情報がリアルタイムで可視化されるようになったことは、効率的な人員配置につながっていますし、より的確な生産指示を実現できています。すべて品質の安定と生産性の向上につながっているものと実感しています。 - 想定していなかったメリットはありましたか。
- 随時、受注や進捗の状況をデータで確認できるようになったことはうれしいですね。以前は、専任担当者による月末の手集計まで、さまざまな数値を正確に把握ができなかったのですが、今では営業責任者や製造責任者が、月次売上高や受注残数をいつでも確認できます。受注から製造、出荷までの状況がリアルタイムにデータベースに反映されるようになったことは、営業戦略や月次生産計画の判断に役立っています。
データの連携・蓄積でハイクオリティを目指す
- デジタル技術を活用して、今後はどんな展開を予定していますか。
-
データベースを一本化したことにより、データの管理・共有が効率化。情報セキュリティもより担保されるようになった。
将来的にはすべての機械設備と生産管理システムを連携させて、稼働状況や稼働実績の可視化とデータ収集を可能にしていきたいと考えています。 その前段階として、昨年は製造のコアプロセスである曲げ工程にネットワーク対応機械設備を導入しました。現在、当該工程では初の試みとなる専用サーバーを介したCAD/CAMによる加工データとの連携、データの蓄積に取り組んでいます。
- デジタル技術の活用を検討している事業者様へ、メッセージをお願いします。
- 今回のデジタル技術の導入で、さまざまな業務においてデジタルの多様な活用法を見い出せました。
業務のデジタル化において、同業他社や周囲からの情報だけに振り回されて、システムありきで進めることはおすすめしません。従業員の力量や抱える課題にマッチしたシステムを導入することが、短期間で期待する効果を得るためのポイントになると思います。
システム導入を支援した方からのメッセージ
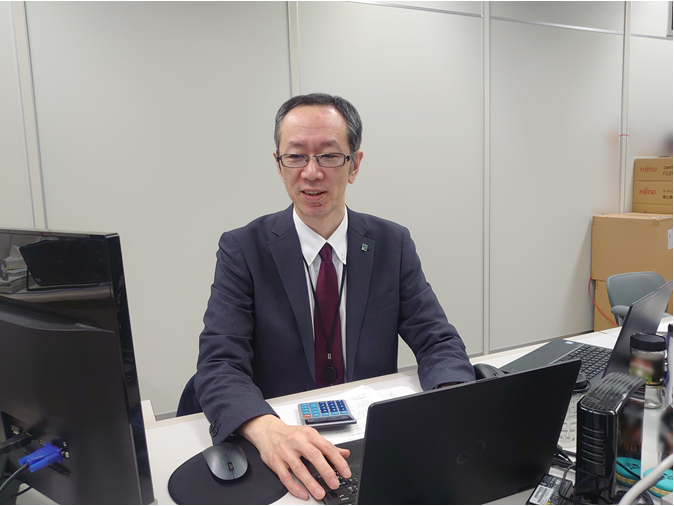
株式会社フィデア情報総研
IT事業本部 民需営業部 課長
佐藤 曜
今回のプロジェクトに際し、マシナリー様より提示いただいた、属人化回避ための「受注情報管理の効率化」と「進捗管理方法の改善」という目的達成に向け、先ずは現状運用の可視化や現場視察を実施しました。
その上で運用に支障なくITの導入効果が得られるか、工場長や現場の方々とともに取り組んだことが、稼働後に効果を得ることができたものと考えております。
(外部サイトに移動)
実際に活用した支援制度(補助金など)
- IoT等先進技術導入実証事業費補助金(秋田県)