生産管理システム・タブレット導入で紙を大幅削減
リアルタイムな進捗管理でリードタイム短縮に成功
株式会社田代製作所
主任
長谷部 秀直
さん
株式会社田代製作所(外部サイトに移動)
分譲マンション向けを中心に木製のドアやドア枠を製造し、日本トップクラスのシェアを誇る「株式会社田代製作所」。細かなオーダーに対応して製造する中で、個当たりの製作時間の短縮や製作指示書のコピー時間・費用の削減等の生産性の向上が課題となっていたことから、<独自の生産管理システム開発><工場内へのタブレット端末導入>に取り組みました。
紙中心の業務体制をデジタル化で一新
- 導入したデジタル技術について教えてください。
-
独自の生産管理システムを開発し、工場作業員一人につき一台のタブレット端末を導入しました。
工程の進捗状況の確認と製作指示書の閲覧がリアルタイムで共有できるようになったほか、受注から出荷までの期間を最大約1日短縮させることができました。
また、工場内作業員に紙で配付していた製作指示書(設計図)をタブレット端末への送信に変更したことで、毎日1~2時間かかっていたコピー作業の大幅な削減に成功し、工場配布用コピー費用を70%~80%削減しました。
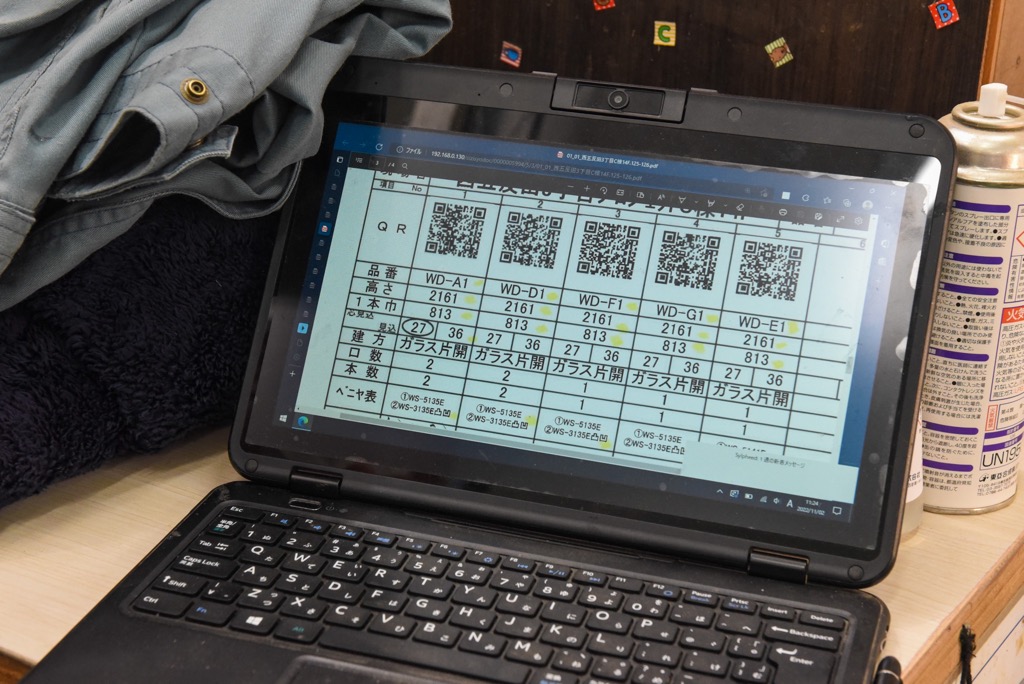
タブレットは木材加工による粉塵に対応した防塵仕様
- 以前の体制では、どのような問題がありましたか?
-
工場内作業員に製作指示書を配付するために、多くの時間とコストをかけていました。
一つの製品につき、約70部のコピーが必要だったため、事務所にある4台のコピー機の内、2台をフル稼働させていました。使用する紙の量は、コピー用紙の納入業者の方が驚くほどでした。
また、以前の体制では、お客様から仕様変更や出荷日の変更があった際の対応にも課題がありました。事務所側では、工場に対して製作指示書の修正版の作成、70部の再コピーなど、工場へ変更があった旨の連絡が必要になります。一方、工場側では、新たに作成された指示書を受け取るため作業員が度々工場と事務所を往来しなければならないため、作業停止が余儀なくされていました。また、工場内で差し替え前後の指示書が混在し、最新版を探す手間がかかったり、誤って差し替え前の指示書で製作したというトラブルが発生したりすることがありました。
さらに、作業進捗を管理するため、毎日終業後にExcelで工場内の進捗状況を確認していました。進度について手動でセルを色分けした出荷予定表を、コピーして作業員に配るという作業があり、こちらにも時間がかかっていました。
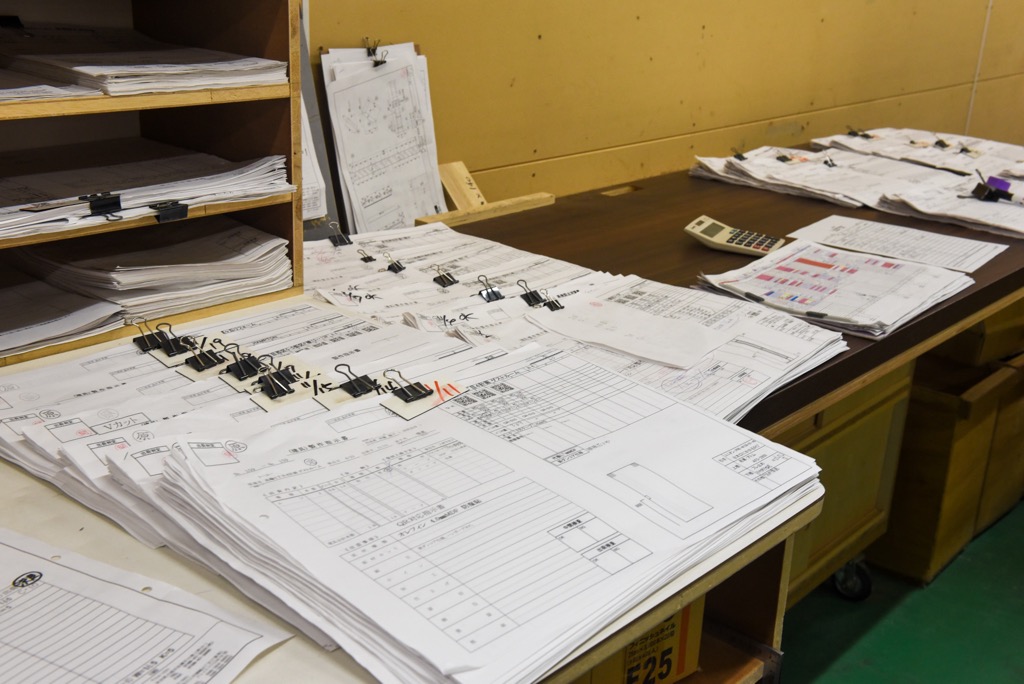
工場内に大量にあった紙の指示書も、今では決められた管理場所にまとめられている
- デジタル技術を導入したきっかけは何ですか。
-
大量の紙の使用によって起こっている様々な問題に対して、どうにかならないかと考え始めたのがきっかけです。当初は紙の使用量50%削減を目標に、工場内に大画面モニターを設置して進捗管理表を共有する方法で改善を図ろうと社内で検討したところからスタートしました。
- 導入に当たり、何か課題はありましたか。
-
社内にデジタル技術やDXに詳しい人材がいないため、一番最初のとっかかりの段階で誰に相談したら良いのか分からず、計画が頓挫しそうになりました。
最終的には株式会社フィデア情報総研様に導入を支援していただけることになり、当社の課題を総合的に検証した上で、独自システム開発とタブレット端末の導入による作業効率化とコピー費用の削減を提案していただきました。
導入の過程でも、支援担当者が話しているデジタル関連用語や内容が分からないなどの苦労がありましたが、伴走型の支援で丁寧な対応をしていただき、業務部や工場からの様々な要望・意見を取り入れた生産管理システムを構築することができました。
製作指示書のデータ化により様々な課題が改善
- 導入前との違いをどのように評価していますか。
-
事務所で作成した製作指示書のデータを、工場内に配付したタブレットに送信することで、当初の目標を上回るコピー用紙の削減を達成しました。コピー作業に追われていた事務員が他の業務を請け負うことができるようになったほか、工場と事務所間の往復で発生していた無駄な移動コストや作業停止時間を削減することができました。仕様変更への対応についても、指示書の差し替えによるトラブルのリスクが減り、作業負荷が減りました。工場作業員にとっては、当日に紙の製作指示書が配られるまでその日何を製作するのか分からない状況でしたが、今では指示書が早い段階で閲覧できるようになったことで、製作の段取りや準備時間が十分確保できるようになり、リードタイムの短縮にもつながっています。
また、ペーパーレス化によって工場内と作業場の整理整頓が図られるようになりました。その結果、作業中の事故や不良品率の低下が見込めます。
そして、各工程が完了後に進捗状況をタブレット端末に入力する仕様に変更したため、業務終了後に工場からの報告を待って集計・作成していた出荷予定表の作成業務の手間がなくなったうえ、リアルタイムな工程の進捗把握ができるようになりました。この工程管理表は、関東営業所の社員も閲覧可能となっており、工場の生産状況の把握や、納期の調整に役立っています。
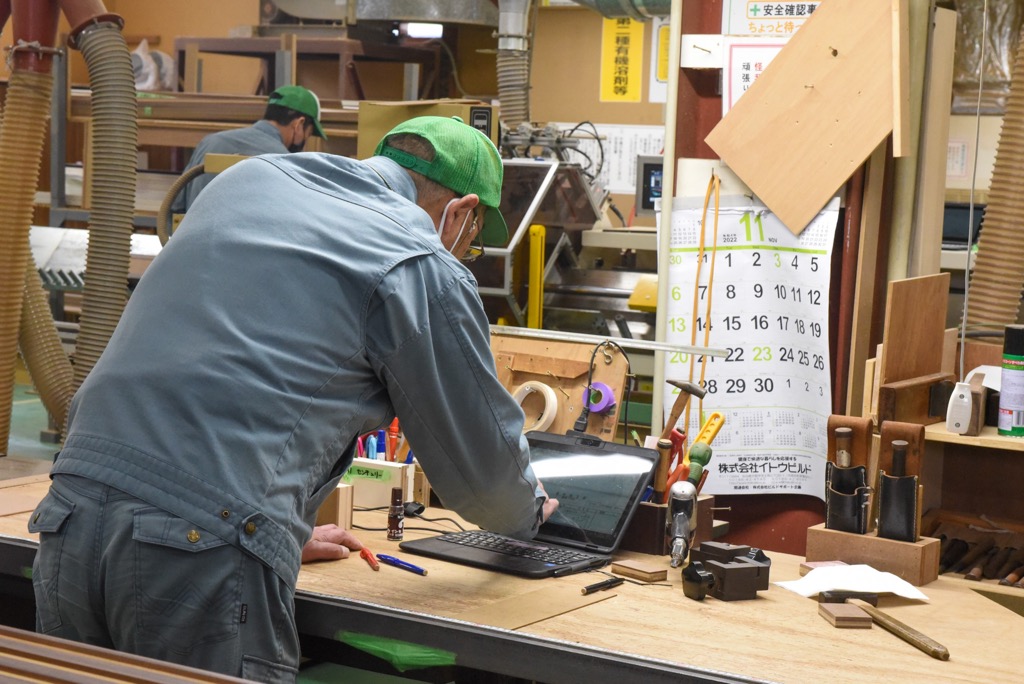
紙が全くなく整頓された作業場
- 導入前には想定していなかった使い方やメリットがあれば教えてください。
-
社内での通達事項などをタブレット端末に配布することが可能になり、情報共有体制の強化につながりました。以前は事務所などに紙を張り出して情報共有していましたが、今は製作指示書と同様、伝達事項を記載したデータを各タブレットに送信することで作業員に確認してもらうことができるようになりました。
- 導入にあたって工夫された点は何ですか。
-
各作業員が必要事項を書き込む際、キーボードではなくペンを使用することで、これまでの紙の指示書と同様の作業効率を保てるようにしました。また、指示書はPDFを活用しているため、書き込みも含めて保存可能です。以前作った製品を再受注した際などに、指示書を探しやすくなった上、書き残しているメモを参照することができます。
また、実際にタブレットやシステムを使用する作業員から要望や意見、感想などを聞き取り、フィードバックするため、従業員全員にアンケートを実施しました。デジタル化への不満等は多少ありましたが、スマートフォンの操作に慣れている従業員も多いことから、想像していたよりはすんなりと受け入れてもらえたと感じています。
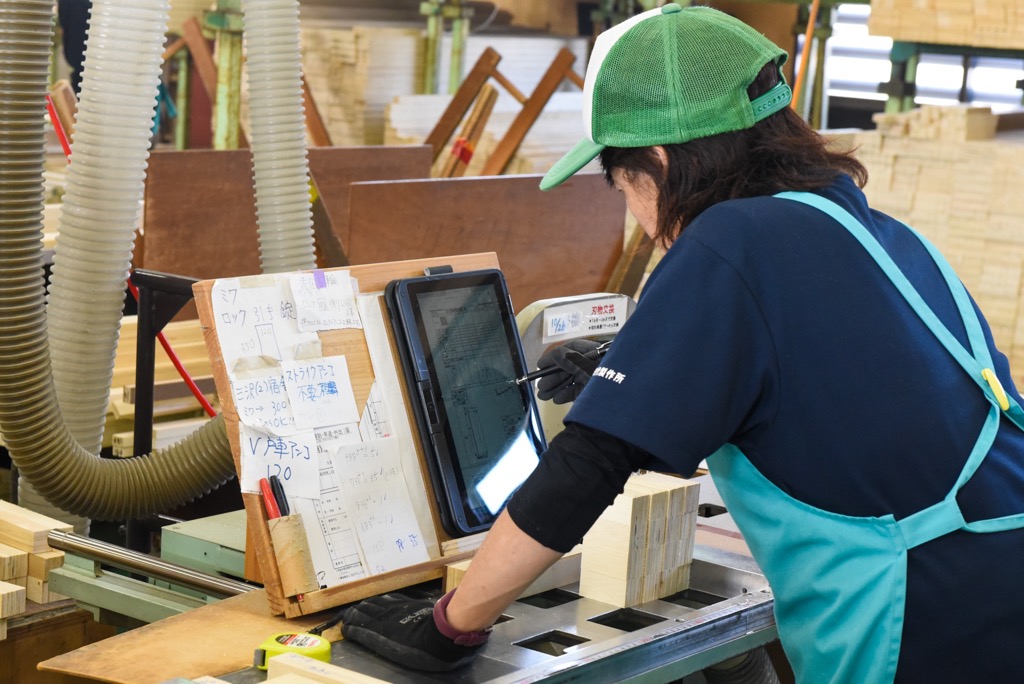
使い慣れた様子でタブレットを操作する作業員
早期の伴走型サポートで効果の高いデジタル化を
- 今後はどんな展開を予定していますか。
-
今回、従業員がタブレットを使用して作業することが当たり前の環境にしたことで、デジタル化推進のための基盤が整いました。今後は、デジタル化を前提として、より一層の業務効率化に取り組んでいくことができると考えています。
製作指示書を作成する業務にシステムを導入し、効率化を図りたいと考えています。お客様からの注文はメールで届きますが、現行の方法では、お客様ごとに異なる発注書の内容を自社で統一した製作指示書のフォーマットに転記する作業が必要となり効率が悪いため、システムの導入で解決しようと現在取り組んでいる最中です。
また、ペーパーレス化の面では、工場内での紙の使用量は大幅に削減できましたが、事務部門などではまだ紙が残っています。紙でなければ作業しにくい部分もあるため、完全にペーパーレスにすることはできませんが、さらなる紙の削減を今後の課題としています。
- デジタル技術の活用を検討しているほかの事業者様へメッセージをお願いします。
-
自前による開発は、まず何から手を付けたらよいのか分からないことが多いと思います。今回のデジタル技術導入で分かったことですが、信頼できるサポート企業から早期に伴走型のサポートをしてもらうことをおすすめします。
当社の場合は、何から手を付けて良いかも分からない段階でフィデア情報総研様に相談したところ、社内の課題をより複合的に網羅したうえで独自システムの開発をご提案いただきました。早い段階から支援者に相談することで、よりニーズに即したデジタル化に取り組む事ができると思います。
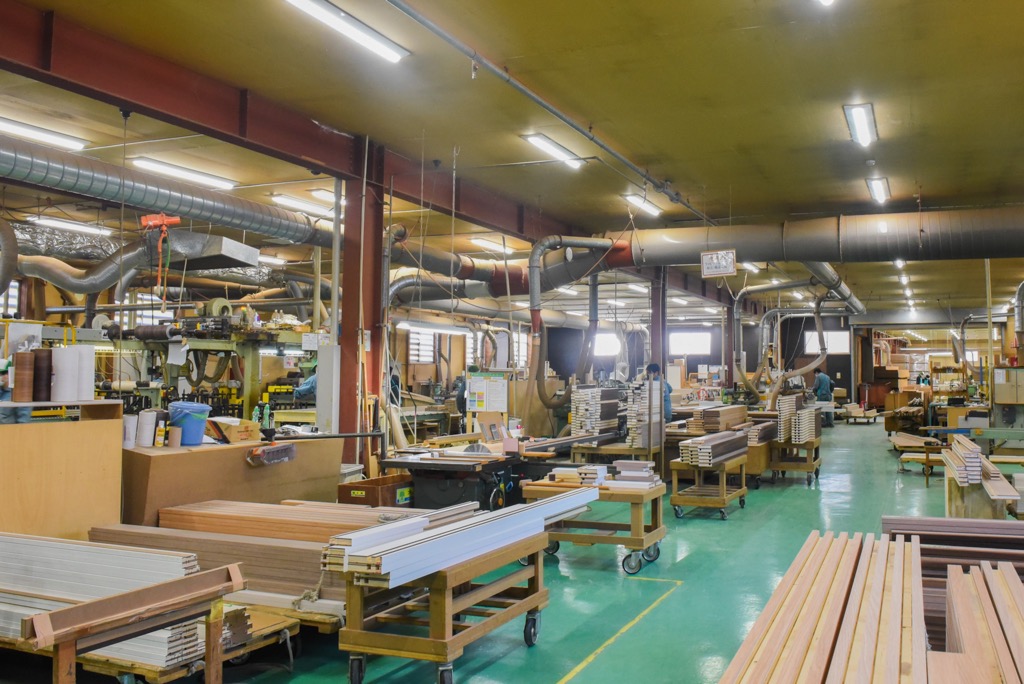
システム導入を支援した方からのメッセージ
株式会社フィデア情報総研
IT事業本部 民需営業部
水谷 太志さん
「ペーパーレス」、田代製作所様の課題は明確でございました。
弊社が、工程表示の大画面や、工場に防塵タブレット数台配置(制作指示書参照用)を提案した際、『数台ではなく全員にタブレットを配布する方向で』と、ご連絡頂いたときは大いに驚いたことを記憶しております。
システム開発の要件定義においても、イレギュラーケースは「無理にシステム化しない」ことをご推奨し、プロジェクトをご牽引頂きました。
今まで、紙の制作指示書に手書きをして後方工程へ伝えていた伝達事項を、PDF化した後でも同じように手書きペン入力を行うことで、運用を大きく変えることなくスムーズにタブレット運用に切り替えられたと思います。
地元秋田で伴走型にてDXに向けたご支援をさせて頂きましたが、無事導入が完了できたのも、田代製作所様の課題に対する強い推進力の賜物と思っております。
(外部サイトに移動)